В Петербурге создали радикально новый вид транспорта
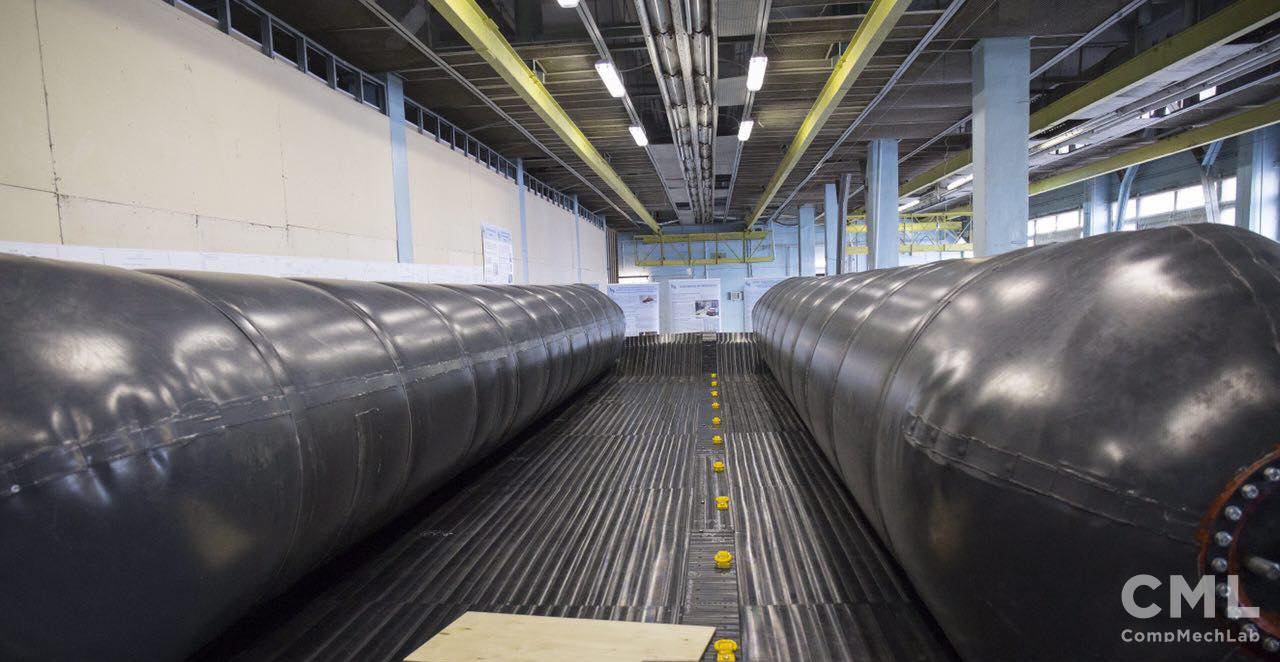
В Петербурге создали уникальные «Антарктические сани» — металлокомпозитные сани для перевозки крупногабаритных и тяжёлых грузов, весом до 60 тонн (РБК Петербург рассказывал о проекте в августе). Первую в мире платформу, которая может перемещать крупногабаритные грузы в Антарктиде разработали и изготовили Центр НТИ СПбПУ и «НПО по переработке пластмасс им. «Комсомольской правды». Об этом сообщили руководители проекта — руководитель Центра НТИ СПбПУ, руководитель Инжинирингового центра «Центр компьютерного инжиниринга» (CompMechLab®) Алексей Боровков и генеральный директор «НПО по переработке пластмасс им. «Комсомольской правды» Сергей Цыбуков в ходе презентации деталей изделия на площадке завода.
Собираться сани будут непосредственно в Антарктике — в январе 2019 года возле антарктической станции «Прогресс». После этого начнутся ходовые испытания уникального транспортного средства, а первая опытная партия будет готова к 2020 году — к 200-летию открытия Антарктиды.
В рекордные сроки
Заказчика саней и характер перевозимого груза руководители проекта не сообщают, ссылаясь на конфиденциальность этой информации. Утверждают только, что заказчик не имеет отношения к Минобороны и грузы — не военные. Судя по составу участников совещаний по проекту, заказчик по-видимому относится к нефтегазовой сфере.
Проект «Разработка прицепного устройства (транспортных саней) из полимерных материалов для транспортировки крупногабаритных грузов (модулей) в Антарктиде» был реализован в рекордно короткие сроки. Заказ получен в мае 2018 года и сдан к 1 ноября 2018 года. Как сообщил РБК Петербург Алексей Боровков, при выполнении такого заказа традиционными методами — только на проектирование ушло бы больше года.
Сложность заказа обусловлена особыми требованиями к изделию. Сани предназначены для перевозок в Антарктиде тяжелых крупногабаритных грузов весом до 60 тонн на расстояния порядка 1,5 тыс. км. Конструкция и материалы саней должны выдерживать экстремальные условия. Во-первых, погодные: температуру до -60 градусов, сильно разреженный и сухой воздух, интенсивная солнечная радиация, сильные порывы ветра и продолжительный ветер. Во-вторых, транспортные — подъемы и спуски по пересеченной местности, изобилующей ледяными застругами и торосами и др.
«Сейчас в таких условиях 60 тонн никто не может перевезти: перевозят грузы до 16-20 тонн, на металлических санях, на лыжах. Но как только лыжа проваливается — она ломается, груз снимается, конструкция ремонтируется, только затем груз идет дальше», — сообщил Сергей Цыбуков.
Эффект двойника
Как он утверждает, рекордные сроки исполнения заказа удалось соблюсти исключительно благодаря проектированию, за три месяца выполненному командой Центра НТИ СПбПУ «Новые производственные технологии» и группы компаний CompMechLab под руководством Алексея Боровкова. Проектировщики применили технологию, опробованную в ходе создания лимузина для президента Владимира Путина в рамках проекта «Кортеж». Технология базируется на уникальной CML-цифровой платформе CML_Bench по разработке цифровых двойников (DigitalTwin, SmartDigitalTwin) с помощью CML-системы интеллектуальных помощников CML_AI, позволяющей выполнять за сутки несколько сотен виртуальных испытаний изделия и материалов для достижения целевых характеристик и удовлетворения всем ограничениям производства.
«Американцы делали аналогичный проект три года, и у них это развалилось. Мы считаем, что они не учли все моменты. Мы не знаем наверняка, что будет с нашими санями, но благодаря «цифровому двойнику» мы будем точно понимать, где у нас возникла проблема, и найдем ее решение. Тот, кто первым в мире сможет перевозить большие грузы, тот и будет иметь перспективу в Антарктиде и Арктике», — уверен Сергей Цыбуков.
Сани на тракторах
Сани состоят из жесткой металлической рамы размером 10 на 12 м, на которую монтируется груз. Рама крепится на особых рессорах — восемь продольных амортизирующих баллонов с воздухом. Они будут гасить продольные и поперечные неровности почвы и обеспечат плавность хода. Функцию лыж выполняет индивидуальная для каждого баллона скользкая пластина, сделанная из особого металлокомпозитного материала. В снегопад над платформой и баллонами натягивается тент. Все используемые материалы способны выдерживать температуру до -60 градусов. Сани несамоходные. В качестве тяговой силы выступят три мощных трактора, мощностью в 300 л.с., давно проверенные в условиях Антарктиды.
По словам Алексея Боровкова, технология его инжинирингового центра и команда проектировщиков не имеют аналогов в России (по этой причине, похоже, ей и поручили проектировать машины для проекта «Кортеж»). Главное достоинство — сокращение в несколько раз сроков проектирования, за счет замены натурных испытаний конструируемого изделия виртуальными в модели цифрового двойника. «На нынешнем этапе промышленного производства сроки выпуска новой продукции определяются главным образом временем проектирования (включая испытания), — утверждает Алексей Боровков. — Изготовить спроектированное изделие можно за две недели». По его словам, скорость вывода на рынок новых изделий в мире выросла настолько, что без использования цифровых двойников угнаться за мировыми конкурентами российским промышленникам уже невозможно.
Цифровые двойники — способ выжить
Продемонстрированные командой Боровкова возможности воодушевили промышленников — и сейчас инжиниринговый центр имеет около 70 заказов на проектирование изделий для предприятий из около 10 разных отраслей промышленности. Крупные заказы выполняются для Росатома и концернов нефтегазового машиностроения — проектируется оборудование для добычи полезных ископаемых, способное заместить попавший под санкции импорт. «С помощью технологии цифровых двойников мы имеем шанс догнать мировых лидеров, производящих оборудование для нефтегазодобычи. Традиционными способами это сделать уже невозможно. Но из-за санкций нам нужно, в сущности, создавать отрасль, которой у нас по большому счету нет», — утверждает Алексей Боровков.
Есть среди заказчиков и петербургские. Так, «Средне-Невскому судостроительному заводу» команда Боровкова помогает создавать цифровую верфь, для «СПМБМ «Малахит» — проектировать подводные лодки. Также из петербургских заказчиков Алексей Боровков называет «ОДК-КЛИМОВ», «Газпром нефть», ПАО «Звезда» и др.
По его словам, смириться с необходимостью («сопротивлялись до последнего») использовать технологию цифровых двойников промышленников заставила жизнь. «Он видит, что теряет конкурентоспособность, поскольку мировые конкуренты в рекордно короткие сроки выводят на рынок новые продукты, а он не может за ними угнаться. Каждый год отставание накапливается и он понимает, что через 5-10 лет его на рынке просто не будет, — поясняет мотивацию промышленников Алексей Боровков. — Сейчас самая острая проблема российской промышленности — отсталое проектирование. Но именно сюда на нынешнем этапе мирового промышленного развития переместилась главная конкуренция». Впрочем, эксперт подчеркивает, что все это касается только тех компаний, которые работают в рынке. Те, кто может без особой конкуренции существовать на госзаказе, не напрягаются и работают по-старинке.