Где лесной промышленности найти резервы для роста
Леспром восстанавливает объемы производства после падения из-за санкций. Как отрасли решить проблемы с оборудованием и кадрами, говорится в исследовании консалтинговой компании ФЦК
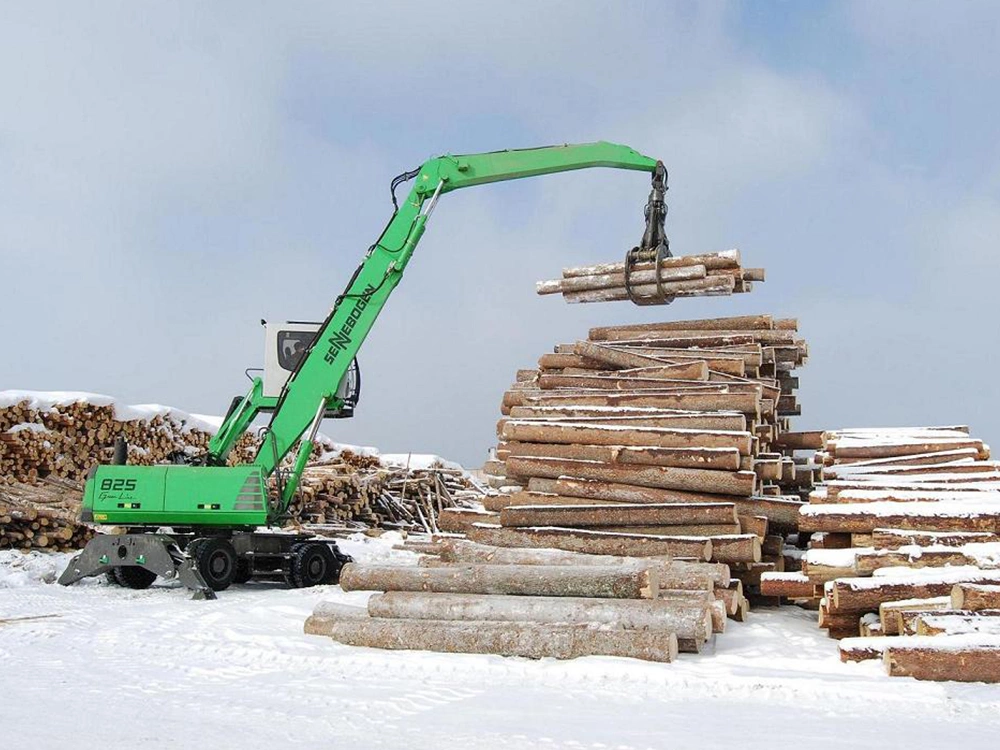
erid: F7NfYUJCUneP4zYih7VP
Дерево вновь пошло в рост
По данным аналитиков из «Делового профиля», в 2023 году лесопромышленный комплекс (ЛПК) РФ произвел продукции более чем на 2,8 трлн руб. Почти 22% оборота пришлось на пиломатериалы; за ними в топ-3 следуют производство мебели и целлюлозы. В «Деловом профиле» уточняют, что предприятия были ориентированы на экспорт (в основном за границу идет фанера и хвойные пиломатериалы), но в 2023 году поставки за рубеж продолжили сокращаться. По сообщению Федеральной таможенной службы, в 2023 году из РФ было вывезено древесины, изделий из нее и целлюлозно-бумажной продукции на $9,9 млрд (на 29,7% меньше показателей 2022 года). В аналитическом центре «Транслес» подсчитали, что за девять месяцев 2024 года экспортные железнодорожные перевозки пиломатериалов снизились на 9% год к году (до 7,3 млн т). Крупнейшим зарубежным рынком для этого вида продукции остался Китай: на страну пришлось 5,3 млн т, или 76% отгрузок (на 11% ниже показателей января—сентября 2023 года).
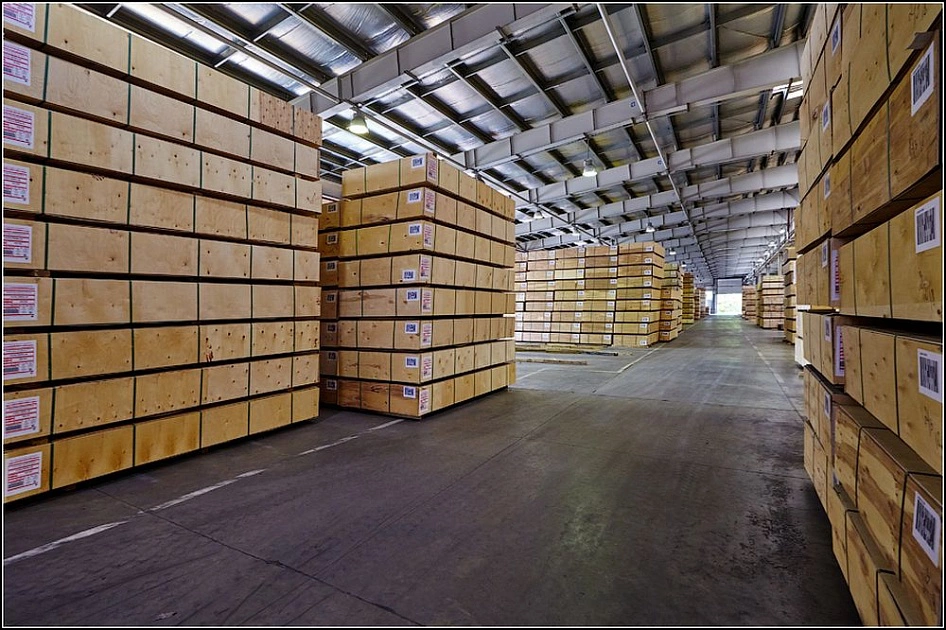
Но несмотря на это, в России началось восстановление ключевых показателей ЛПК. По данным Росстата, в январе—апреле 2024 года производство пиломатериалов выросло на 1,1% год к году (до 9,7 млн кубометров), фанеры — на 14,5% (до 1,17 млн кубометров), бумаги и картона — на 10,1% (до 3,5 млн т). Правда, итоги первых десяти месяцев этого года скромнее: объем производства пиломатериалов, по данным Росстата, вырос год к году лишь на 0,2% (до 23,9 млн кубометров). За это же время производители произвели 2,84 млн кубометров фанеры — на 4,7% больше (в сравнении с январем—октябрем 2023 года). В «Деловом профиле» подчеркивают, что основные индексы работы ЛПК в РФ «начали оживать» в первом квартале 2023 года и перешли к росту в середине прошлого года. Руководитель Рослесинфорга Павел Чащин заявлял, что отрасль восстановилась после санкционного шока и показала «уверенный рост», в том числе благодаря выходу на новые рынки.
В ФЦК напоминают, что Россия входит в тройку крупнейших мировых производителей ЛПК, но по уровню производительности труда в отрасли находится на шестом месте (после США, Китая, Канады, Австрии и Японии). В пример в ФЦК приводят годовую производительность труда в пересчете на работника в американском ($250 тыс.), китайском ($170 тыс.) и российском ЛПК ($100 тыс.). В «Деловом профиле» уточняют, что по запасам лесных ресурсов Россия — первая страна в мире (1,19 млрд га, или 82 млрд кубометров).
Развитие предприятий отрасли ограничивают традиционные проблемы: среди них устаревшее оборудование, удаленность от транспортной инфраструктуры и недостаточная квалификация рабочих кадров. В ФЦК проанализировали эти трудности, представив в базе знаний рекомендации для индустрии. В исследовании, в частности, упоминаются модернизация производственных процессов, развитие человеческого капитала и внедрение цифровых технологий, в том числе телеметрии и системы управления запасами, позволяющих исключить потери сырья. «Мировые примеры показывают, что автоматизация и устойчивое управление ресурсами — ключевые аспекты успеха в деревообработке. Россия обладает колоссальными лесными ресурсами, и мы считаем, что, следуя современным стандартам, а также применяя бережливые технологии, отечественные компании смогут значительно улучшить свои показатели», — подчеркивает один из авторов исследования, заместитель гендиректора ФЦК по аналитике и методологии Алексей Курушин.
Опыт набирает обороты
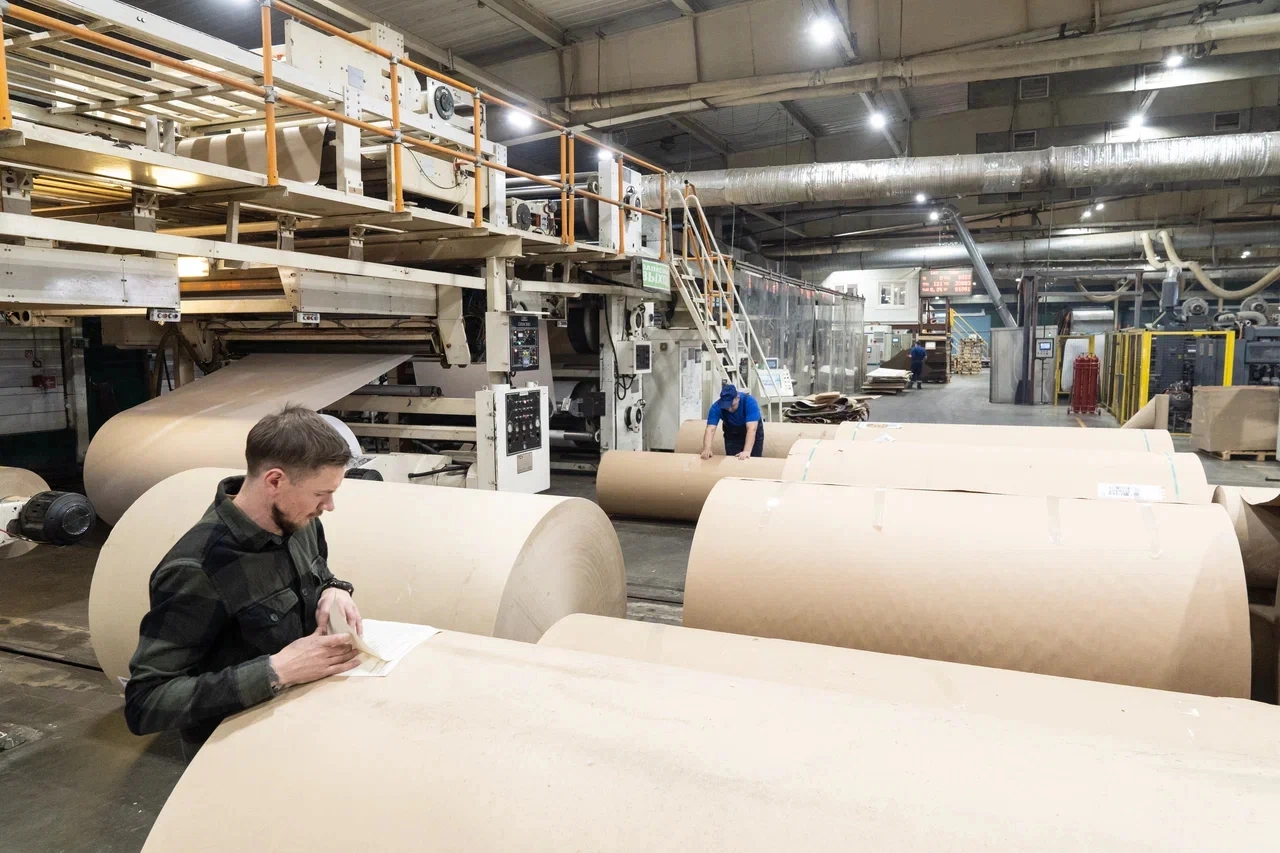
В ФЦК подсчитали, что производительность труда в рамках одноименного нацпроекта удалось повысить на 240 предприятиях деревообработки с суммарной выручкой более 560 млрд руб. В этих компаниях внедрялись принципы бережливого производства, позволившие 114 участникам нацпроекта увеличить совокупную добавленную стоимость на 26 млрд руб., а производительность труда — в среднем на 36%, подсчитал Алексей Курушин. В ФЦК пояснили, что наиболее эффективно себя показали мероприятия по стандартизации процессов и перебалансировке загрузки оборудования и персонала.
Так, компания «Севлеспил» из Коми за счет участия в нацпроекте увеличила выработку фанеры на 48% и уже получила дополнительно 100 млн руб. выручки. Потенциальный экономический эффект, по расчетам экспертов ФЦК, оценивается в 600 млн руб. в год. «Мы на 77% снизили уровень запасов, а время производства одной партии пиломатериалов у нас сократилось на 72% — с тридцати до восьми с половиной суток», — рассказывает гендиректор «Севлеспила» Татьяна Миронова.
Производителю пиломатериалов из Кировской области — Вятскому фанерному комбинату — удалось в рамках нацпроекта уменьшить количество брака на предприятии. По словам начальника отдела развития производственной системы Алексея Седова, Вятский фанерный комбинат столкнулся с «узким местом» на линии сращивания. «Провели несколько видов хронометражей и увидели, что операторы тратят слишком много времени на уборку линий, к тому же получается много отходов шпона. Так как станки на линии находятся на высоте около 2 м, то неподходящий лист шпона просто скидывался оператором на пол, часто ломался и шел в дробилку. Организовали оператору место для хранения, так что теперь неподходящие листы шпона аккуратно перекладываются слева от станка, а получившуюся пачку забирает погрузчик», — рассказал Алексей Седов. По его словам, оптимизация процесса позволила получать с одного станка на 4,2 кубометра шпона больше, что составляет 7–8% от суточного производства. «Снизили коэффициент расходов сырья на 6 куб. м с потока», — добавил Алексей Седов. Опыт работы с ФЦК в рамках нацпроекта, безусловно, оказался полезен, добавил он: «Мы провели обучение в рамках бережливого производства, что помогло в дальнейшем лучше идти на контакт с сотрудниками. Ведь обычно рабочие тяжело реагируют на изменения, внедряющиеся на предприятиях». Предприятие продолжает оптимизацию за счет рационализаторских идей от работников комбината, отметили в ФЦК.
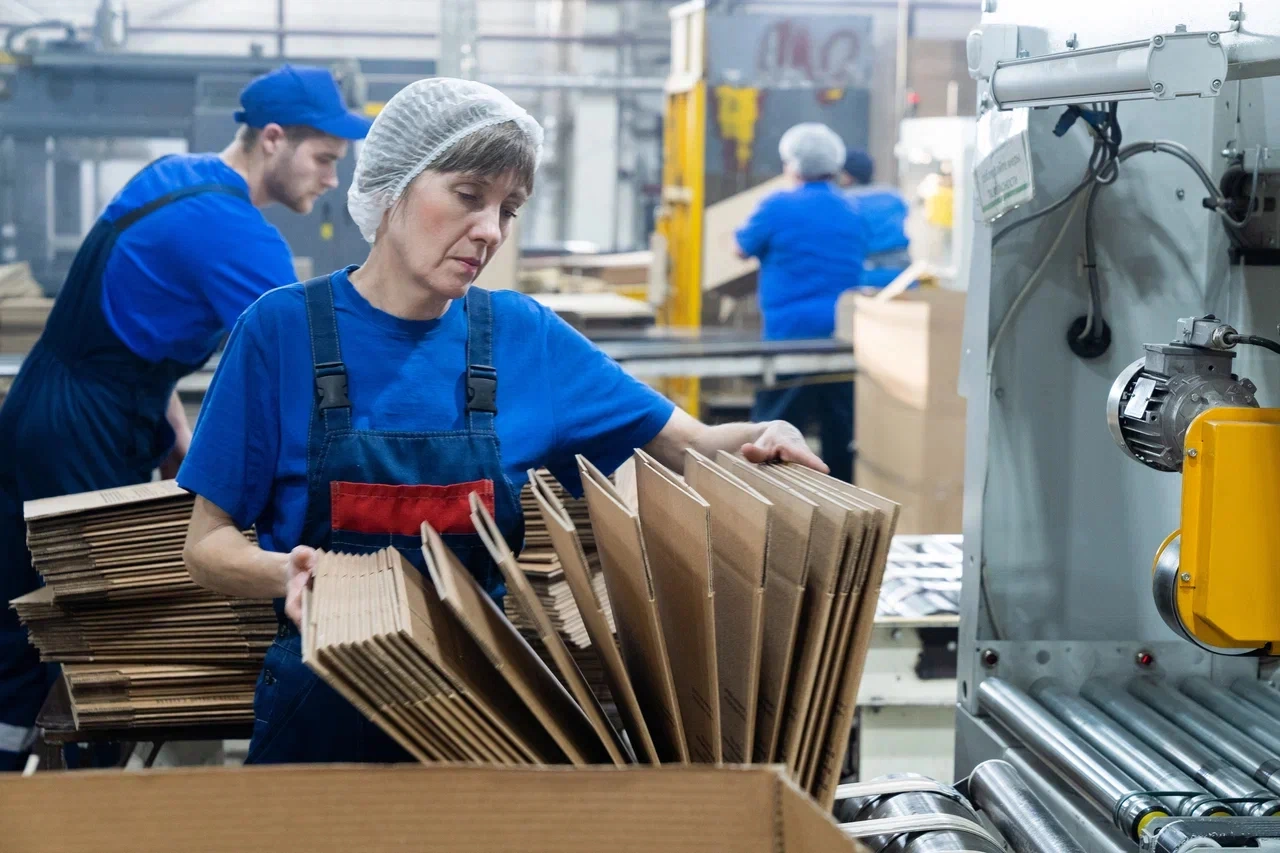
Хорошо зарекомендовало себя бережливое производство и на новосибирском предприятии «Болотнинская гофротара»: в рамках нацпроекта выработка гофрокартона там была увеличена на 66%. Заместитель гендиректора по производству предприятия Полина Фесикова рассказала, что в нацпроект компания пришла с запросом снижения количества простоев и увеличения уровня доступности оборудования. «Сперва мы внедрили классификатор простоев, содержавший семь категорий и 42 подкатегории. На части линий переработки у нас уже были автоматические датчики и контроллеры, передающие данные в программу управления предприятием — туда мы «вшили» классификатор, и при каждом простое на экране наладчик должен был указать его причину», — поделилась менеджер. По ее словам, это позволило сократить простои из-за отсутствия деревянных поддонов, установив систему их автоматической подачи, разместив стенд с инструментами рядом с оборудованием и стеллажи для хранения материалов, а также введя должность помощника наладчика оборудования. Также, по словам Полины Фесиковой, была перестроена система планирования производства. «Если ранее мы старались более ровно загрузить гофроагрегат, то сейчас сместили акцент на равномерную загрузку линий переработки по вытягивающему принципу», — говорит менеджер. Кроме того, по ее словам, на предприятии переделали промежуточный склад гофрозаготовки, выделив зоны под каждую линию по принцу FIFO («первым пришел — первым ушел»), а сами заготовки стали хранить не в деревянных поддонах, а в металлических профилях — под размер вил погрузчика. В итоге, по словам Полины Фесиковой, производительность труда на предприятии увеличилась на 47%, уровень загрузки оборудования удалось довести до 85%, а время его переналадки — уменьшить более чем на 40%. Экономический эффект от участия в нацпроекте в «Болотнинской гофротаре» оценили в 54 млн руб. в год.
Директор компании «Готэк Северо-Запад» Сергей Бородин рассказал о совместном с ФЦК опыте оптимизации линии производства четырехклапанного ящика из гофрокартона. «Командой была выстроена карта потока создания ценности, она позволила проанализировать каждый шаг производства и выявить все потери. Куратор ФЦК помог подобрать нужные инструменты для сокращения этих потерь. Например, визуализация мест хранения. В зоне незавершенной продукции мы нанесли разметку, что привело к сокращению времени поиска заготовок с десяти до двух минут. Запустили три смены работы гофроагрегата, что позволило равномерно распределить заготовку по линиям переработки — это сократило количество незавершенной продукции с 8 тыс. до 7 тыс. кв. м. Сократили дистанцию транспортировки продукции, что позволило исключить из потока два погрузчика. Пересмотр технологических режимов производства заготовки сократил время «отлежки» материала с 20 до 15 часов. Совокупность проведенных работ сократила цикл производства на четыре дня. Мы сэкономили 4 млн руб. на снижении объема незавершенной продукции, 12 млн руб. — за счет оптимизации складов, на 1,4 млн руб. сократили фонд оплаты труда», — рассказывает Сергей Бородин. По словам менеджера, после совместного проекта с ФЦК его предприятие распространило принципы бережливого производства и на остальное оборудование. «Есть идеи, как развивать это в дальнейшем, правда, они требуют более серьезных инвестиций», — говорит Сергей Бородин.
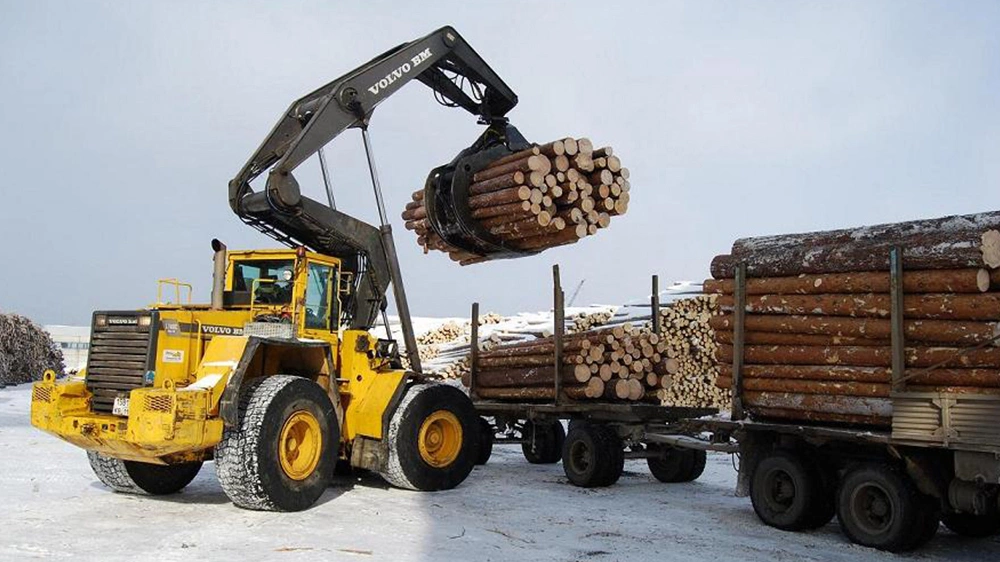
Помимо внедрения бережливого производства, в ФЦК рекомендуют усиливать глубину переработки сырья и по возможности диверсифицировать производство, поясняя, что при «просадке» одного вида продукта можно будет переключиться и увеличить объем выпуска более востребованного. В исследовании экспертов также говорится о производстве инновационных продуктов как трендов ближайшего будущего в деревообработке (например, древесной пены и композитов с применением древесины) и о том, что программы переквалификации работников могут обеспечить рост продуктивности предприятий на 20–30%. «Развитие лесопромышленной отрасли требует комплексного подхода, объединяющего модернизацию, цифровизацию и повышение квалификации персонала. Следуя лучшим мировым практикам, отечественные компании могут значительно сократить производственные потери, повысить конкурентоспособность и при этом минимизировать воздействие на природу», — резюмирует Алексей Курушин.
Напомним, российские компании из базовых несырьевых отраслей экономики начиная с 2025 года смогут повышать свою производительность труда в рамках нового национального проекта «Эффективная и конкурентная экономика».